Steel is the largest carbon-emitting industrial sector and one of the fastest-growing sectors in India in terms of both economic output and carbon emissions. India is the world’s second-largest producer of crude steel with a total production of about 120 million tons per annum (MTPA). However, India’s per capita consumption of steel is just one-third of the global average, and one-fifth of the average of developed countries. With economic growth, domestic demand for steel is expected to rise rapidly in the coming decades. To meet this demand, the Ministry of Steel, under the National Steel Policy (NSP), has set an ambitious target of reaching 300 MTPA capacity / 255 MTPA production by 2030. By 2040, the demand is projected to increase further by 3 – 4-fold from current levels.
As per CPI’s analysis, the steel sector currently contributes to 7 – 10% of India’s total CO2 emissions[i]. A rapid growth in output would result in a steep increase in emissions from the sector, which are expected to double by 2030 in a business-as-usual scenario. Given the long lifetimes of steel plants (usually 30 years and above with re-lining) and the high emission intensity of production, it is imperative that the sector adopts lower-carbon means of production and gradually shifts to carbon-neutral pathways. This is imperative for India to achieve its net-zero emissions target by 2070, and the world to achieve climate goals set out under the Paris Agreement.
In this article, we use data[ii] on Indian steel plants and global green steel projects to analyze new production capacity that is planned to be added to the Indian steel sector, low-carbon technologies (LCTs) being adopted for green steel production globally, and sources of funding for these LCTs. Through this analysis, we aim to inform stakeholders about the expected emissions from the Indian steel sector the potential role of emerging LCTs, and the differentiated roles of the public and private sectors in driving steel decarbonization in India.
India set to build at least 200 MTPA of new fossil-based emission-intensive steel production capacity over the next 15 years
As of March 2023, the Indian steel sector had about 195 MTPA of steel production capacity in the pipeline (either ‘announced’ or ‘under construction’) that is due to start production over the next 15 years, until 2038. To provide a sense of scale, this is more than the current steel production capacity of the US, UK, Germany, and France combined. Figure 1 below shows the annual estimated capacity addition segmented by the type of production route.
The capacity consists of both integrated steel plants as well as individual BOF and EAF units[iii]. Nearly one-third (66%) of the new capacity will be added as the BF – BOF route, 9% as the DRI (coal-based) – EAF/IF route, 16% as a combination of BF, DRI, BOF, and EAF/IF, and the remainder is unknown. Nearly 90% of the capacity is estimated to go online by 2030, contributing towards meeting the domestic demand for steel needed to fuel India’s economic growth. However, from an emissions perspective, these trends are worrisome.
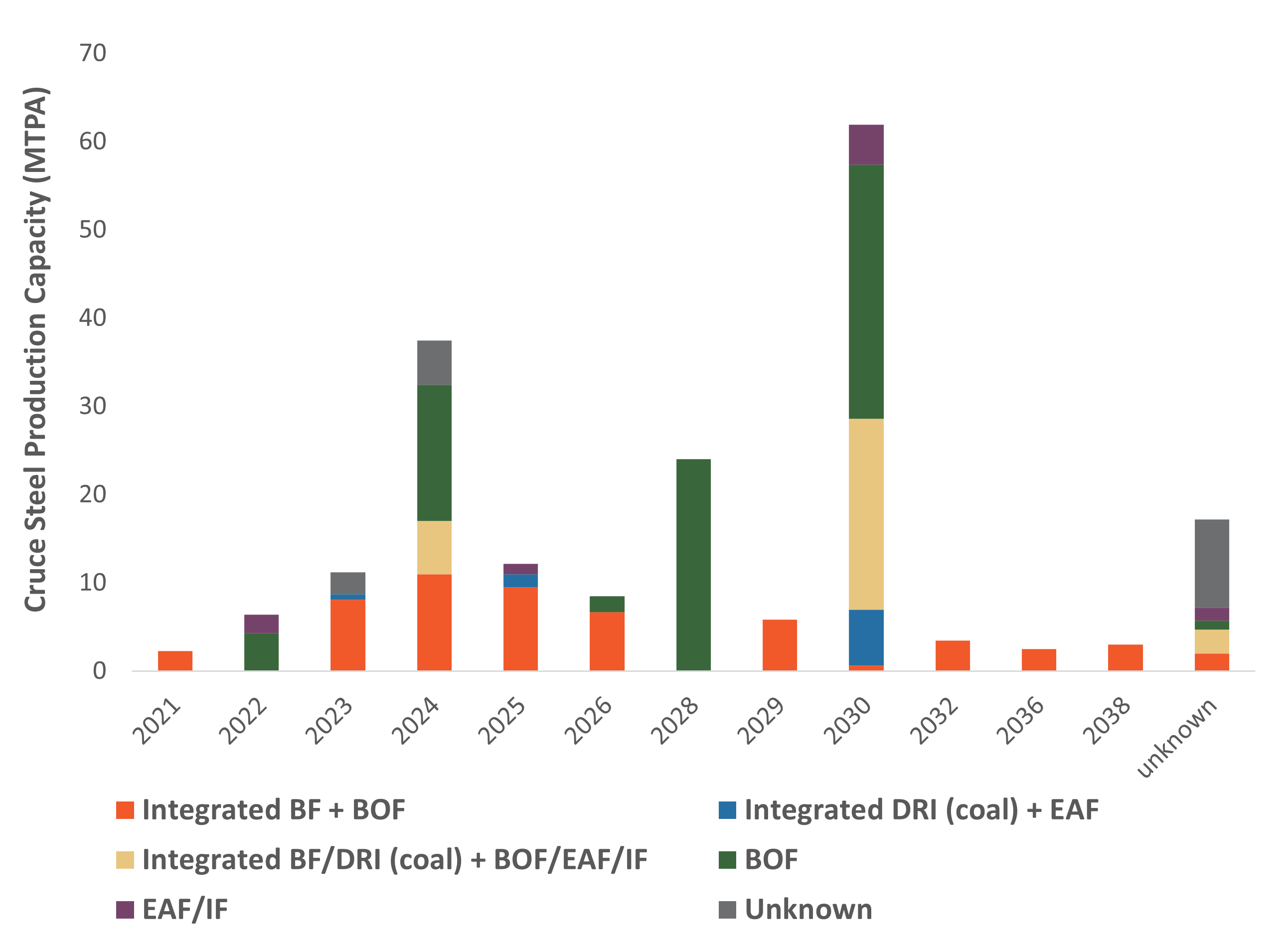
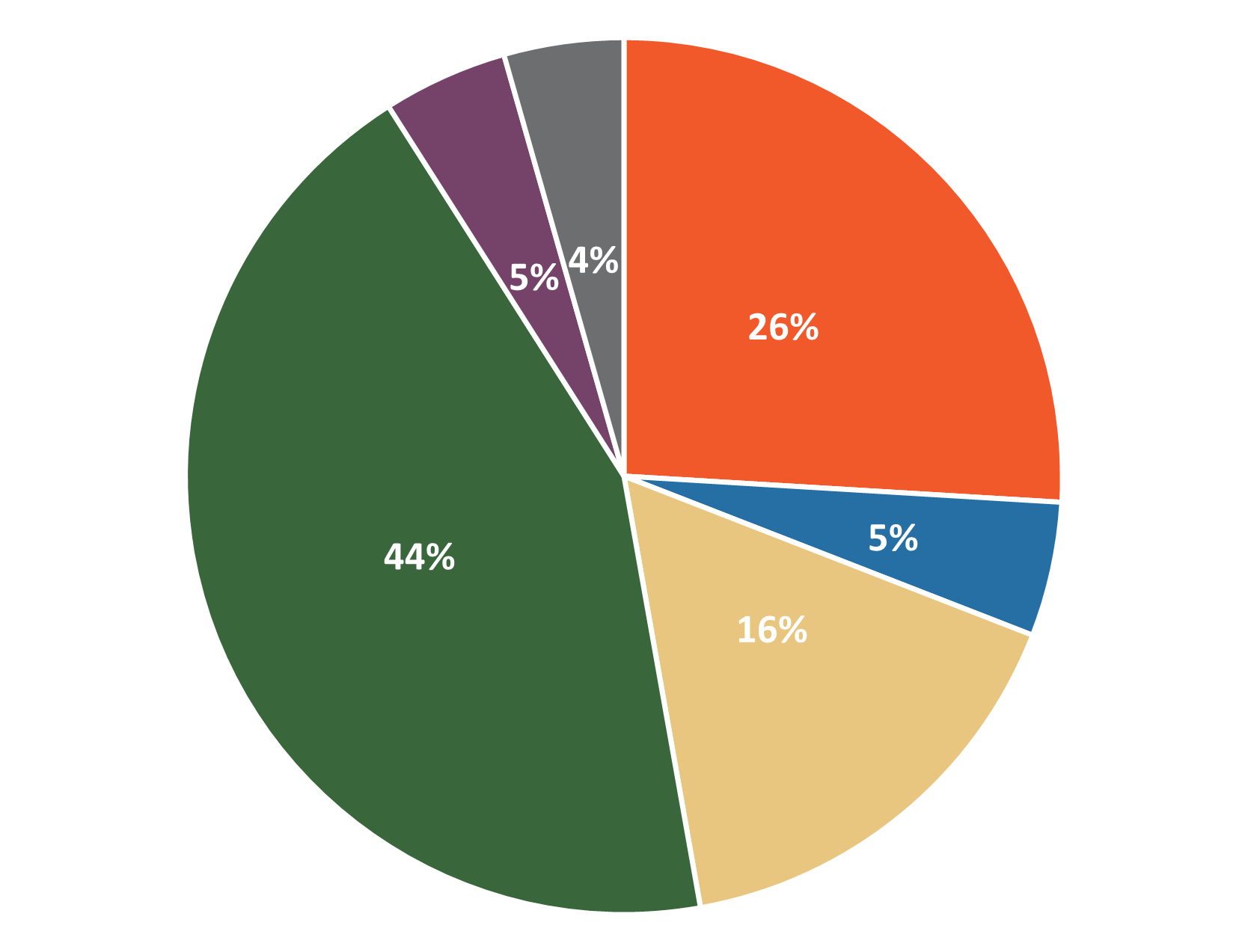
Figure 1 (a): New crude steel production capacity in India ‘announced’ or ‘under construction’, estimated to start production by 2038. Figure 1 (b): Distribution of the new crude steel production capacity in India by type of production route.
The Indian steel sector’s average emission intensity and annual carbon emissions are expected to rise rapidly. Furthermore, the planned addition of BF – BOF capacity would increase the total cost and complexity of decarbonizing the sector.
As per current plans, nearly all of the new production capacity that is expected to be added is fossil-based (i.e., via. BF – BOF and DRI – EAF/IF route. Only a small share of the same is through scrap-based EAF units). As per our analysis, this will increase the average emission intensity (of all production routes) of the sector from 2.18 tonne of CO2/tonne of crude steel (tCO2/tcs) currently, to 2.27 tCO2/tcs (ignoring any improvements in energy efficiency). Therefore, the emissions from the sector are expected to increase at a faster rate in the coming years. As a result, the total annual emissions would more than double from 260 MtCO2 per annum currently to 560 MtCO2 per annum by 2030. This presents a massive decarbonization challenge for the Indian steel industry, and the world at large.
The distribution of planned production capacity further highlights the complexity of the challenge. The majority of new capacity to be added is via the BF – BOF route (resulting in an increase in its overall share in the capacity-mix from the current 45%, the rest being DRI – EAF/IF). While this trend may be driven by issues such as availability and quality of minerals – lower grade iron ore available in India is primarily suited for utilization in the BF – and limited availability of scrap to meet the growing domestic demand, it has major long-term implications for emissions trajectory of the sector.
The BF – BOF route is much harder to decarbonize than the DRI – EAF route. Decarbonizing the BF – BOF route would most likely require adoption of Carbon Capture and Storage (CCS) technologies (unless there are major technological breakthroughs) since other levers such as injection of green hydrogen in the BF and increasing scrap utilization in the BOF are limited by technological considerations. CCS technologies have a higher cost of abatement (especially when CO2 storage is included) compared to other LCT alternatives such as hydrogen-based DRI (for more details on LCTs, see our previous blog). Therefore, an increasing share of BF – BOF is likely to increase the long-term dependence on CCS, and thereby increase the overall cost and complexity of decarbonizing the steel sector.
Globally, investments of over USD 30 billion have been announced in various technologies to produce green steel.
The main technologies for production of green steel that are attracting investments are: hydrogen-DRI (H-DRI), carbon capture utilization and storage (CCU/S), and scrap-based EAF. As of April 2023, a cumulative investment of USD 32.25 billion has been announced in projects amounting to 40 MTPA of green steel production capacity, 15 GW of green hydrogen production capacity, and 3 MTPA CO2 capture capacity. These projects are due to come online over the next 10 years. While this is significant, it is far short of the USD 200 billion needed annually for investments in low-carbon technologies to achieve a net-zero steel sector globally by 2050, as estimated by the Mission Possible Partnership.
Figure 2 below shows the distribution of planned investments by technology and the scale of the project. Using publicly available data, we also tracked and analyzed the source of funding for these projects[iv]. Figure 2 also shows the division of investments by public and private sources of funding.

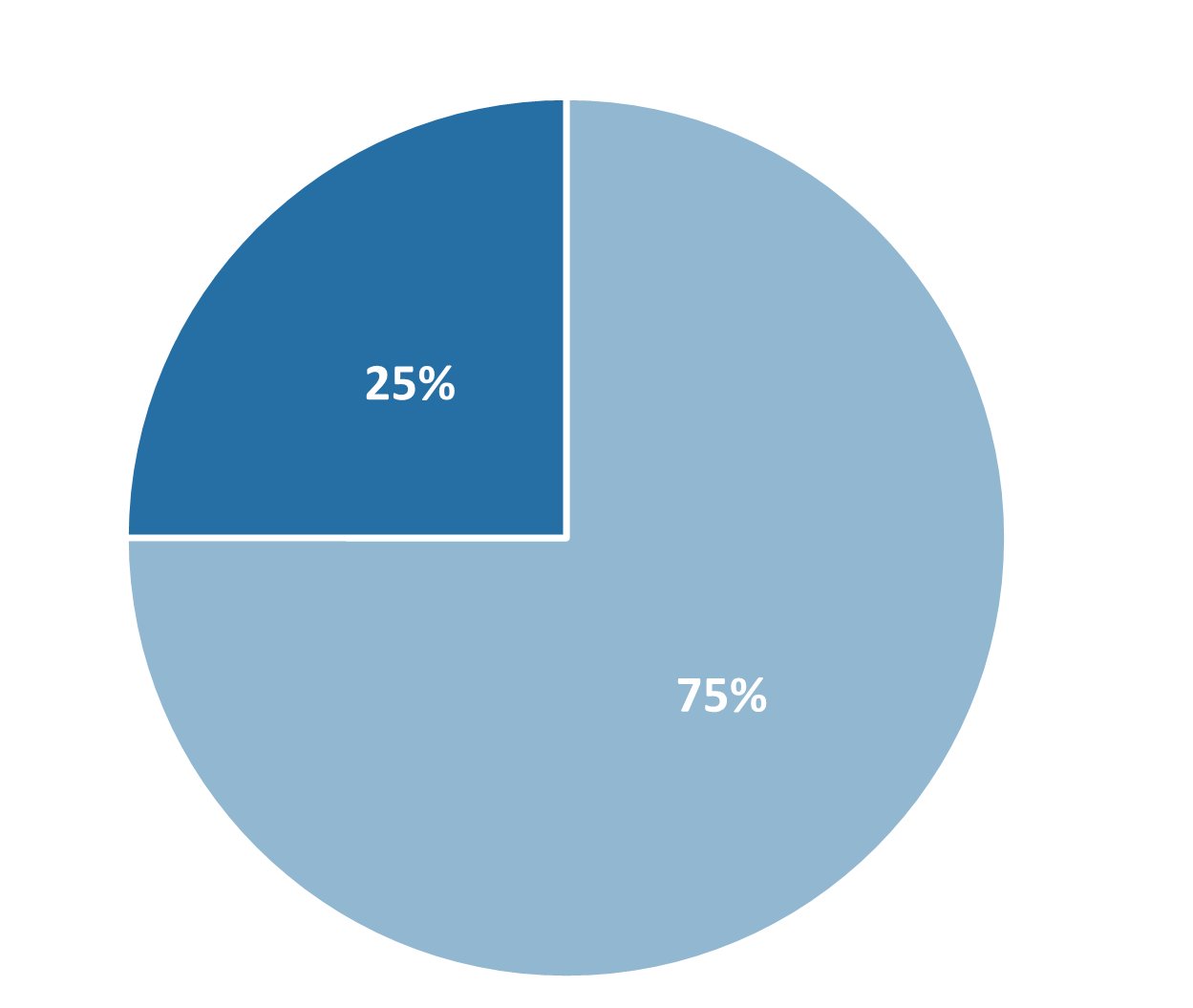
Figure 2 (a): Global investments in green steel production by technology and scale of production. Figure 2 (b): Distribution of public and private sources of funding for green steel projects.
Hydrogen-DRI (H-DRI) is the leading technology for green steel production and would likely play a critical role in decarbonizing the Indian steel sector.
Globally, H-DRI – EAF accounts for about 83% of planned investments in green steel production (either in steel plants or in hydrogen production for utilization in steel plants), followed by scrap-based EAF (13%), CCU/S (3%), and others (1%). Geographically, most of these investments have been announced in the EU (85%), followed by Canada (6%), Australia, Norway, Russia (2% each), S. Korea, and the USA (1% each). Furthermore, over 90% of these investments are in full-scale plants[v], signaling mitigation of technology risks and graduation of emerging LCTs to TRL 8-9[vi] (commercial operations) in these geographies.
H-DRI – EAF is emerging as the leading LCT for steel decarbonization. This is likely due to policies implemented in the EU (e.g., a carbon pricing, carbon-border adjustment mechanism), large-scale public-funded innovation programs implemented in several countries, lower cost of abatement compared to CCU/S, and limited reliance on scrap steel compared to scrap-EAF route. H-DRI – EAF is likely to witness high rates of learning and cost decline (and therefore increasing competitiveness against conventional routes), which could make it a preferred technology for adoption by Indian steel makers in the coming years.
Other factors such as India’s push on green hydrogen (framed under the National Green Hydrogen Mission), limited clarity on pathways for deployment of CCU/S technologies, and lack of availability of sufficient quantities of scrap steel, would also contribute to a shift to H-DRI – EAF route over the long-term. The projected BF – BOF dominated growth of the Indian steel sector is misaligned with a potential H-DRI – EAF led decarbonization trajectory for the sector. However, this may change as green hydrogen costs decline and policy mandates on green hydrogen consumption are put in place for the steel sector, which is likely after 2030.
Public funding and carbon pricing are supporting the deployment of emerging breakthrough technologies in the early stages of industrial transition.
Breakthrough LCTs needed for steel decarbonization are currently commercially unviable in the absence of supportive policies and regulations for green steel production (such as green steel definition and standards, investment subsidies, guaranteed offtake with premium, etc.). They have a high cost of abatement (at least 50 – 60 USD/tCO2) and would significantly increase the cost of production of steel. Furthermore, because of the competitive nature of the industry, high capital intensity, and long lifetime of assets, there is a high level of inertia in the industry to stick to conventional processes. Therefore, appropriate incentives need to be provided to steel companies through direct public funding and market-based mechanisms to unlock private investments in breakthrough LCTs.
Our analysis shows this to be true. Globally, public funding accounts for a substantial 25% of investments in green steel production, proving to be the source of early-stage risk capital for emerging technologies and thereby catalyzing investments by the private sector. Public funds are being deployed as innovation grants, subsidies (viability gap funding), or equity (as co-investments) for the development of supporting infrastructure (e.g., for hydrogen transportation and storage), and for improving the economic viability of green steel projects. Carbon markets are also an important source of revenues for many projects, especially in the EU, where the carbon price under EU-ETS has been ranging between 80 – 100 EUR/tCO2 in recent times. In comparison, the indirect carbon price under the Perform Achieve and Trade scheme (PAT Scheme) in India was found to be just 0.5 – 4 USD/tCO2[vii] during PAT Cycle II (2016 – 19).
India’s national policies for the steel sector would need to consider the allocation of public finance for supporting first movers investing in green steel projects. Specifically, patient risk capital would be needed for creating an enabling environment and improving the risk-return profile of investments in demonstration and first-of-a-kind commercial scale projects. However, given fiscal constraints, a limited amount of public capital needs to be deployed strategically to achieve the maximum catalytic effect. Domestic public funds could be complemented by international climate finance, to meet the demand for billions of dollars in green and transition finance needed by the sector. In addition, India would also need to ensure that the national carbon market (which is under development) is designed, implemented, and regulated well to attain carbon price levels that reflect the cost of abatement for breakthrough technologies in industrial sectors and can thereby incentivize a shift towards green steel production. For more details on supportive policy frameworks, see our policy brief.
While there may be scope for breakthrough innovation by new ventures, the Indian steel sector’s decarbonization pathway would be dictated by a few large corporations.
Globally, several steel companies have planned investments in green steel production. These are (by investment volume): ArcelorMittal (26%), H2GreenSteel (17%), Blastr Green Steel (13%), Thyssenkrupp (8%), Liberty Steel and Salzgitter (6% each), and others. While the majority of the investments are led by large corporates, investments in new ventures such as H2GreenSteel, Blast Green Steel, and Boston Metal (which together account for a third of all investments) demonstrate that there is scope for disruptive breakthrough innovation, provided there is a functioning enabling ecosystem in place.
In India, the steel sector is dominated by a few large companies. JSW Steel, TATA Steel, Steel Authority of India (SAIL), Jindal Steel and Power (JSPL), and ArcelorMittal/Nippon Steel (AM/NS) account for over 75% of current and over 70% of the planned production capacity. Therefore, actions taken by just five large companies in the coming years will likely dictate the decarbonization pathway for the entire Indian steel sector. The nature of innovation in the steel sector (high capital intensity, technology complexity, and long development periods) does not align with the risk-return expectations of traditional early-stage investors. Therefore, to enable breakthrough innovation in sectors like steel, the ecosystem for innovation would need to be strengthened. Effective use of innovation policies to create an enabling environment, large-scale public and privately funded programs that provide technology commercialization support (e.g., ArcelorMittal’s XCarb Innovation Fund and Accelerator which supports startups with funding and industry partnership), and patient venture capital models (e.g., Breakthrough Energy Ventures) are needed.
Note on assumptions:
Assumptions | Values |
Average emission intensity | BF + BOF = 2.5 tCO2/tcs DRI (coal) + EAF = 2.8 tCO2/tcs DRI (gas) + EAF = 1.4 tCO2/tcs Scrap-based EAF = 0.6 tCO2/tcs |
Share of scrap in steel-making | BOF = 20% EAF/IF = 80% |
Average plant lifetime | 30 years |
Capacity Utilization Factor | 85% |
[i] Varies depending on the methodology used.
[ii] Data sourced from Global Energy Monitor (GEM) on steel plants and the Leadership Group for Industrial Transition (LeadIT)
[iii] BF = Blast Furnace; BOF = Basic Oxygen Furnace; DRI = Direct Reduced Iron; EAF = Electric Arc Furnace; IF = Induction Furnace
[iv] Public data on source of funding was available for about 50% of the total investment volume.
[v] The database uses company reporting to identify the innovation stage of projects – R&D, pilot, demonstration, and full scale. Since classifications varies between companies, there is no single reference scale of capacity by which projects have been classified.
[vi] TRL = Technology Readiness Level (TRL)
[vii] PAT scheme is targeted towards energy savings rather than CO2 emissions. Here we converted the price of energy savings certificates or ESCerts to an equivalent price on carbon: Carbon price (USD/tCO2) = ESCert price (USD/toe)*total energy savings (toe))/total CO2 reduction (tCO2).